MÉTODO DE WASHBURN
O Método de Washburn é uma abordagem experimental para avaliar a molhabilidade de materiais granulados e pós. Permite entender como líquidos diversos interagem com partículas sólidas em sistemas pulverizados e granulados. A aplicabilidade do Método é muito ampla. É utilizado para a avaliação da eficiência do molhamento de materiais particulados de interesse para as indústrias farmacêutica, química e de processamento mineral, particularmente na separação de fases pelo processo de Flotação. Compreender o molhamento de pós e granulados é crucial para prever o comportamento das partículas quando entram em contato com um líquido. Para muitas aplicações no processamento de cerâmicas, argilas, formulações farmacêuticas ou cosméticas e no processamento mineral compreender e quantificar a eficiência da molhabilidade é essencial para a otimização dos processos envolvidos.
As abordagens de medição direta de ângulos de contato líquido-superfície não podem ser usadas em materiais sólidos pulverizados (pós e granulados). Ficam evidentes as limitações experimentais e de representatividade estatística caso se desejasse medir o ângulo de contato seguindo a metodologia que é utilizada quando a superfície do sólido é suficientemente grande para acomodar uma gota individual do líquido molhante. (Figura 01).

Essa limitação é contornada recorrendo ao método desenvolvido por Edward W. Washburn que recorre à medição da taxa de ascensão do líquido de interesse em um tubo de diâmetro reduzido contendo o material pulverizado.
O método de Wasburn permite calcular o ângulo de contato a partir da taxa de ascensão do líquido no tubo usando a seguinte fórmula:
cos θ = (Dh)/(ηL)
onde:
θ é o ângulo de contato entre o líquido e as partículas de pó.
Dh é a taxa de ascensão do líquido no tubo, ou seja, a altura da coluna líquida que é ascendida na unidade de tempo.
η é a viscosidade dinâmica do líquido.
L é a tensão superficial do líquido.
Vale ressaltar que esta equação não leva em consideração fatores como a geometria do capilar ou a variação da taxa de ascensão com o tempo. A variação da taxa de ascensão depende de inúmeros fatores e deve ser considerada em casos específicos.
O procedimento experimental consiste em medir o tempo que o fluído leva para ascender através de um tubo em que uma das suas extremidades está em contato com o líquido. A ascensão do líquido no tubo ocorre devido à capilaridade, que é influenciada pelo ângulo de contato entre o líquido, a superfície do tubo e o molhamento das partículas do pó inserido no tubo formando uma coluna cilíndrica.
A equação que relaciona o tempo de ascensão (t) com o ângulo de contato (θ) é conhecida como a equação de Washburn:
h = (2γcosθt) /(ρgr)
onde h é a altura da ascensão do líquido (medida em intervalos de tempo definidos), γ é a tensão superficial do líquido, ρ é a densidade do líquido, g é a aceleração da gravidade e r é o raio do tubo.
O avanço da frente de molhamento com o tempo é registrado em gráfico típico, tal como esquematizado na Figura 02.

O vídeo aqui apresentado foi realizado, para fins demonstrativos, durante um experimento para determinação da taxa de ascensão de um líquido em uma coluna de granulado heterogêneo em termos de granulometria e composição mineralógica. A montagem utilizada foi projetada e desenvolvida de acordo com o Método de Washburn (Figura 03).
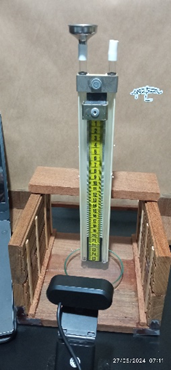
É importante ressaltar que podem existir variações na montagem e procedimentos específicos dependendo do material estudado, do objetivo do experimento e dos recursos materiais disponíveis.
SUGESTÕES PARA LEITURA
Washburn E.W., The dynamics of capillary flow, Physical Review 17 (1921) 273–283.
Kiesvaara, J., & Yliruusi, J. (1993). The use of the Washburn method in determining the contact angles of lactose powder. International Journal of Pharmaceutics, 92(1-3), 81–88.
Kirchberg, S., Abdin, Y., & Ziegmann, G. (2011). Influence of particle shape and size on the wetting behavior of soft magnetic micropowders. Powder Technology, 207(1-3), 311–317.
Kirdponpattara, S., Phisalaphong, M., & Newby, B. M. Z. (2013). Applicability of Washburn capillary rise for determining contact angles of powders/porous materials. Journal of Colloid and Interface Science, 397, 169–176.
Lazghab, M., K. Saleh, I. Pezron, P. Guigon and L. Komunjer (2005). “Wettability assessment of finely divided solids.” Powder Technology 157(1–3): 79‐91.
L. Susana, F. Campaci, A.C. Santomaso, Wettability of mineral and metallic powders: Applicability and limitations of sessile drop method and Washburn’s technique, Powder Technology 226 (2012) 68–77.
Study of Surface Wettability of Mineral Rock Particles by an Improved Washburn Method. Zheng Wang, Yanping Chu, Guozhong Zhao, Zhilin Yin, Tie Kuang, Feng Yan, Lei Zhang and Lu Zhang. ACS Omega 2023, 8, 15721−15729
Wettability Assessment of Submicrometer Alumina Powder Using a Modified Washburn Method. Bram Neirinck, Johannes van Deursen, Omer Van der Biest and Jef Vleugelsw. J. Am. Ceram. Soc., 93 [9] 2515–2518 (2010) DOI: 10.1111/j.1551-2916.2010. 03854.x 2010 The American Ceramic Society
Wettability measurement apparatus for porous material using the modified Washburn method. Manish Thakker, Vikram Karde, Dinesh O Shah, Premal Shukla and Chinmay Ghoroi2013 IOP Publishing Ltd . Meas. Sci. Technol. 24 125902 DOI 10.1088/0957-0233/24/12/125902