The development of new technologies and estrategies in mining and geological
exploration of mineral deposits are close related to the quality of the components of the
drilling tools. Drilling crowns, for instance, are built fixing hard particles (inserts) in a
metallic matrix. Industrial diamonds are usefull as cutting particles impregnated in a
metallic alloy having Cu, Fe, W, Co, as the major elements. In order to have an
excelent performance during drilling an optimum adherence between inserts (abrasive
particles) and matrix combined with the wear rate of the matrix is the challenge of
materials engineering for high quality drilling tools. Industrial diamonds are widely used
as cutting particles and their performance depends on operational parameters and on
the quality of the diamonds (morphology, purity, size distribution,…) and their
adherence to matrix. According to these considerations the main parts of the drilling
crown – the teeth – are sophisticated metal matrix – ceramic material manufactured by
powder metallurgy methods in which pressure, temperature, atmosphere and powder
quality have to be well controlled to achieve good results. In order to contribute to
develop best cutting parts the quality of diamonds plays a distinguished role.
Accordingly to these considerations an experimental method was developed to
characterise the abrasivity of diamonds crystals (natural or synthetic) for this kind of
application. The test configuration is a classic three body tribosystem: counterbody,
abrasive (diamonds) and a rock sample which wear (loss of mass) shows how
efficiently the abrasive is. The method consists in measure the cutting efficiency of
particles (diamonds) against a rock reference sample. The mass loss of this rock
sample is the parameter evaluated along the tests. Depending on diferences of mass
loss rate caused by diferent diamonds, these hard particles can be ranking in terms of
abrasivity – their capability to wear the sample. Results are presented validating the
experimental method: diamonds from diferent suppliers show diferent capacity in
wearing the reference rock body. A microstructural characterisation of the diamonds,
done by SEM, provides informations about their chemical, morphological and structural
quality. In conclusion this method allows to select hard particles for tribological
applications.
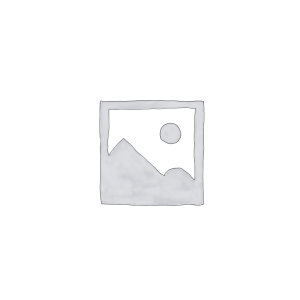
R$35,00
The development of new technologies and estrategies in mining and geological
exploration of mineral deposits are close related to the quality of the components of the
drilling tools. Drilling crowns, for instance, are built fixing hard particles (inserts) in a
metallic matrix. Industrial diamonds are usefull as cutting particles impregnated in a
metallic alloy having Cu, Fe, W, Co, as the major elements. In order to have an
excelent performance during drilling an optimum adherence between inserts (abrasive
particles) and matrix combined with the wear rate of the matrix is the challenge of
materials engineering for high quality drilling tools. Industrial diamonds are widely used
as cutting particles and their performance depends on operational parameters and on
the quality of the diamonds (morphology, purity, size distribution,…) and their
adherence to matrix. According to these considerations the main parts of the drilling
crown – the teeth – are sophisticated metal matrix – ceramic material manufactured by
powder metallurgy methods in which pressure, temperature, atmosphere and powder
quality have to be well controlled to achieve good results. In order to contribute to
develop best cutting parts the quality of diamonds plays a distinguished role.
Accordingly to these considerations an experimental method was developed to
characterise the abrasivity of diamonds crystals (natural or synthetic) for this kind of
application. The test configuration is a classic three body tribosystem: counterbody,
abrasive (diamonds) and a rock sample which wear (loss of mass) shows how
efficiently the abrasive is. The method consists in measure the cutting efficiency of
particles (diamonds) against a rock reference sample. The mass loss of this rock
sample is the parameter evaluated along the tests. Depending on diferences of mass
loss rate caused by diferent diamonds, these hard particles can be ranking in terms of
abrasivity – their capability to wear the sample. Results are presented validating the
experimental method: diamonds from diferent suppliers show diferent capacity in
wearing the reference rock body. A microstructural characterisation of the diamonds,
done by SEM, provides informations about their chemical, morphological and structural
quality. In conclusion this method allows to select hard particles for tribological
applications.
Ainda não há comentários.